
One of the issues I ran into with the first recycled denim tote I made was the lack of rigidity in it’s structure. Visually, I like how it turned out, but I felt it was too floppy. There’s this balance that needs to happen between structure and weight that I’m sure a lot of architects would be familiar with. The thinner and lighter the material, the less stress it can withstand. Another secondary issue involved balancing the relationship between aesthetics and function. More embellishment means more weight and structure, but consequently it also means the bag itself will be heavier.
That first bag went in the direction of lightness, with minimal patchwork and embellishment. But with this one, I pushed a little further into a heavier composition of patchwork that wouldn’t be so floppy. There are of course other ways of approaching the structure issue such as adding thin interior pockets for paper/card stock inserts, or even using starch. My interest in raw denim lead me to that starching idea, I should try it some time.
Looking at various constructions for tote bags lead me to the conclusion that the structure is achieved in two parts. The first is the folded over stage in which the strip(s) of material are formed into a flat, enclosed shape. In the second stage, the bottom is pleated to achieve a three dimensional form. From a design perspective, this was quite liberating. Regardless of how you achieve that first flat stage, the pleating of the second stage will always add structure. So I took a cue from Japanese design, specifically from sakabukuro bags which consist of long strips of fabric, spiral seamed into these fantastic diagonal forms. Some of you may remember I’ve used this technique before on a woven scarf called Delete C.



There was a good amount of measurement I had to do before hand, but it all worked out, and my math proved to be sound. Basically what I needed was a long strip of fabric, and I happened to have a composition that fit the exact width in my calculations. As the weeks went by, that length of patchwork denim grew longer until I had reached the required length.


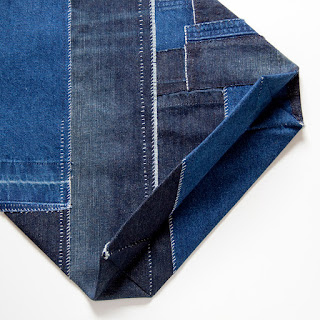
This particular spiral seam consists of an alignment between the center point of the fabric and the center point of the hypotenuse of a 45 degree fold. The fabric is then folded perpendicularly to the hypotenuse until it runs out at the top. I had been working overlapping seams during the patchwork process, so I employed them here on the spiral seam as well. This altered my calculations a bit, but not by much. The hypotenuse of the initial fold then had to be pleated to make the flat ‘foot’ of the bag. I did this on the inside, sewing down the resulting right triangles to get those nice sharp corners.


By the time I got to the handles, I was basically winging it. I didn’t have a plan to deal with those peaks at the top of the bag. Initially, I just wanted to conceal them by folding them inward. Playing with that idea a bit, I decided to fold them in only half way, leaving a nice angular opening on either sides of the folds, but also doubling the fabric where the handles would be sewn in.

When it comes down to it, yes. This tote is more rigid than the last one I made, so in that regard, the goal has been met. I think I can push it further, but the issue isn’t necessarily with the structure, it's with the materials. Denim—especially recycled denim—is broken in, and inherently floppy. That’s it’s charm, but also it’s disqualifier. If I truly want to create rigid structure, what I need to be working with is leather. A patchwork sakabukuro style leather tote. Wouldn’t that be awesome?
Fiber Credits:
Darker denim: Old Navy
Lighter denim: Kikwear
Navy thread: Banana Republic
White thread: Façonnable